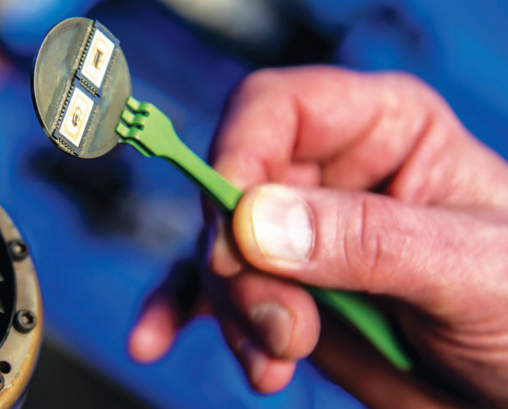
DOE EPSCoR Implementation Grant: Harsh Environment Materials and Fabrication Techniques for Wireless Sensor Applications
PI: Mauricio Pereira da Cunha
Co-PI: Robert Lad
Research Associate: Luke Doucette
Award Amount: $750,000
Award Dates: September 2019 – September 2021
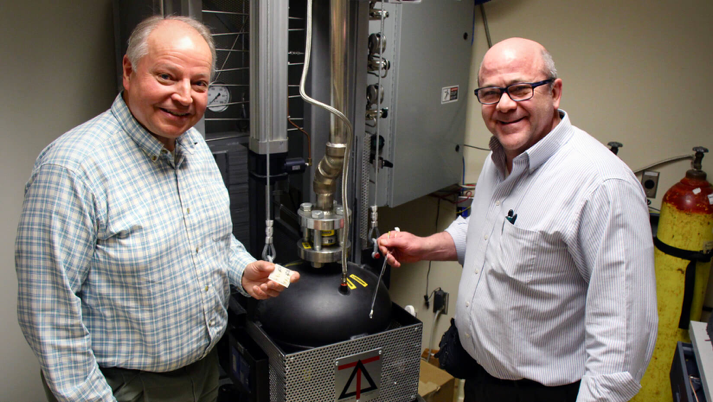
Harsh Environment Sensor Technology and its Impact
Imagine gas turbine engines, like those found on airplanes, or nuclear or coal power plants that experience high temperatures with corrosive and erosive conditions. These engines and power plant systems operate at temperatures capable of melting the metal they are made out of. They require careful structural design, advanced cooling techniques, and temperature monitoring to allow the metal to expand and contract as necessary for the engine to function safely.
Without advanced methods to effectively monitor these temperatures and the strain imposed on the materials involved, the risks and costs involved in the design and operation of components and systems can be prohibitive. Nobody wants a gas turbine engine or a power plant component to fail under operation. Such catastrophic events result in excessive costs, and more importantly, pose unacceptable threats to structures and safety.
This is a significant problem that an interdisciplinary team at the University of Maine is currently tackling. Mauricio Pereira da Cunha, a professor of electrical and computer engineering, and Robert Lad, a professor of physics, are leading a two-year, $750,000 project funded by a Department of Energy (DOE) EPSCoR Implementation grant; one of only nine that were awarded in 2019.
Project Goals to Expand Harsh Environment Sensor Technology
The goal? Create a wireless nano-technology that is able to withstand extreme temperatures up to 1000°C (1800°F) and over 50,000 times the force of gravity on earth, while being packaged in a way that protects the performance of the device, and tiny enough to place on small components; down to 1 mm by 2 mm to be precise. That’s roughly the size of a grain of rice.
“Temperature and strain have to be monitored in order to properly design parts aimed to operate in high-temperature, harsh environments, or predict and detect damage or malfunctions,” Pereira da Cunha says. “The ability to do so remotely, thanks to wireless technology, has a lot of advantages. It can be placed on moving parts, like a rotating blade in a gas or steam turbine, or a moving part on a belt furnace of a production line or process, for example.” This goal may seem insurmountable, but Pereira da Cunha and Lad have been researching and developing this type of technology for about two decades. Their combined expertise has helped make the University of Maine a go-to research hub for harsh environment technology needs, due to the worldwide forefront patented technology created at UMaine.
Economic and High Technology Impact to the State of Maine
The activities generated from past projects resulted in the creation of Environetix Technologies, a custom wireless sensor technology company, located in Orono, ME, which has employed about twenty people since its creation in 2009. Environetix is one of seven different sensor-based companies that have spun out of research originally conducted at University of Maine’s interdisciplinary Frontier Institute for Research in Sensor Technologies (FIRST), which was previously known as the Laboratory for Surface Science and Technology (LASST). These spin-off companies have created hundreds of high paying jobs throughout the years, and have helped to mitigate Maine’s “brain drain” by hiring many talented scientists and engineers graduating from UMaine.
Together with the University of Maine, Environetix has generated services and manufactured products for the U.S. Air Force, the Department of Defense, and the DOE. An important aspect of the past, current and future work in this area, is the mentorship and hands-on training opportunities available to students, engineers, and technical personnel working on these projects. In particular, the group working on this DOE EPSCoR funded project will learn skills in advanced electronic device fabrication, materials analysis, and other laboratory techniques that are directly transferable to meeting the needs within several industries, including semiconductor and biomedical companies based in Maine.
Heading Towards Future Sustainable Infrastructure and Activities
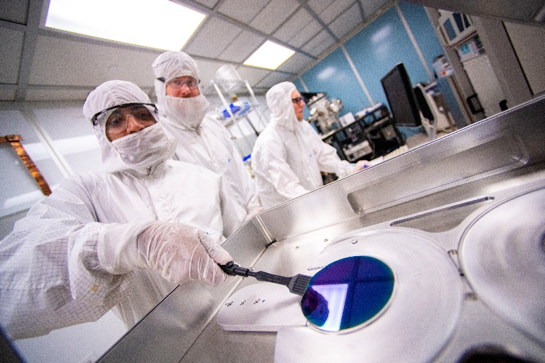
While the challenge of producing a material that is able to retain its conducting and insulating functions under extreme conditions is indeed a difficult task, these two scientists and their expanding team of researchers have the experience and inspiration necessary to achieve it. They are also passionate about involving more scientists from a variety of disciplines in order to look at the challenge from as many vantage points as possible.
Research activities have benefitted from the established capabilities within FIRST. The development of this complex technology includes thin film deposition, clean room microfabrication, nanoscale materials analysis using microscopies, spectroscopies and diffraction; high-temperature thermal processing; and testing of prototype sensor component materials and sensor devices.
Prototypes of this technology have already been placed at the University of Maine Steam Plant, the Penobscot Energy Recovery Center, and Longview Power Plant in West Virginia, and tested in gas turbine engines from General Electric and Rolls Royce. At these types of facilities and applications, the wireless sensor technology will not only improve safety and lower maintenance costs, but also help manufacturers to operate their systems and engines more efficiently, thus reducing fuel usage and the emission of polluting gases. This can be achieved through the sensors’ ability to provide real-time data for parameters such as temperature, strain, pressure, corrosion and gas concentration. For the current project, new developments are planned to broaden the scope of applications and the technology’s efficiency.
The applications for this type of technology far exceed power plants and turbine engines. This nano-technology could easily be applied to ceramic, steel and other metal production, space exploration, oil exploration, the transportation industry, complex engine systems, and other advanced manufacturing processes that involve extreme conditions that will benefit from the ongoing and future scientific and technological advances made at the University of Maine.
“We have the ability to further flourish and expand this technology to new applications, also continuously increasing its impact,” Pereira da Cunha says. “We are seeking additional collaborators and funding to make sure this research and development effort continues to benefit the state of Maine, the U.S., and the world.”