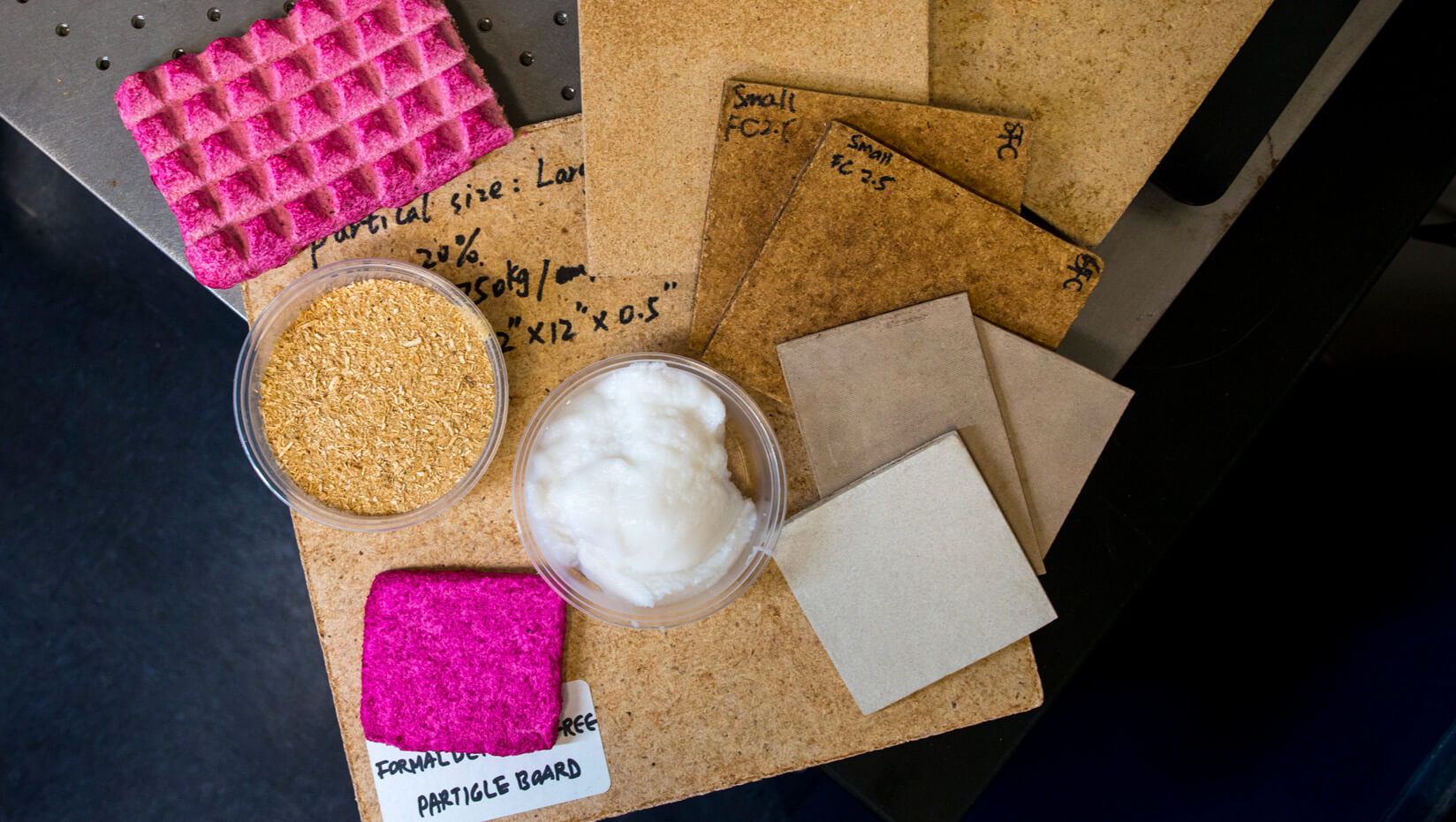
Tajvidi awarded $250,000 to develop next-generation CNF floor, wall products
Transcript
Mehdi Tajvidi:
Cellulose nanomaterials have been around for many years. Because they are produced in water, we need to dry them and then use them like other materials which are normally dry. The fact is drying nanocellulose is very difficult, very time consuming and it’s really energy intensive.
This is our nanocellulose. This has 97 percent water in it at this time. If you want to squeeze the water out using your hand, this is what you get. You can’t.
Now, I’m going to mix this nanocellulose with some wood particles. So now if I try to do the same thing, squeezing the water, this is what you get. See that? So just clear water comes out in your hand and this has very little nanocellulose to it.
Normally, wood composites are made using a binder and that binder is normally a resin and that normally has formaldehyde in it. So, you might have heard about all formaldehyde emissions issues for wood composites.
This technology uses wood as a binder agent for wood. So, basically there is no formaldehyde added here.
This is one example of the University of Maine formaldehyde-free particle board, as you see. So, this is made by just combining wood particles with nanocellulose, removing the water mechanically so we are not using any heat in this stage, and then the final stage is a hot pressing that makes the panel.
We have used the same idea to produce fiberboard panels that are used for like, kitchen cabinets. This is again a prototype basically this would be similar to drywall but this will be really light.
The other product is a flooring system that takes the same idea. We are working with a company that produces a high-end cement product. Very nice material for flooring systems.
These are basically made for wall coverings or wall sheathing.
Maine has always been very proud of its paper and pulp industry but unfortunately that industry is not really doing well. There is a lot of wood material here available to be used but there is not much market for it.
If you replace about 10 percent of the weight of the particle boards that are produced every year in North America with nanocellulose, you’re talking about a potential market of about 400,000 tons of dry nanocellulose every year. So, it’s a huge market.
We are basically turning the low value-added material into a high value-added material now that can help the forest products industry in Maine and elsewhere and also it has many environmental benefits.