Team #8 Bicycle Helmet Brake Lights
Meet the Team
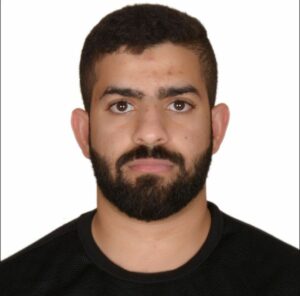
Ahmed Almusharraf is from Saudi Arabia and is currently a senior at the University of Maine who is studying Mechanical Engineering Technology. He transferred to the United States for college after starting his college career in Canada.
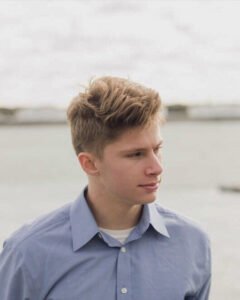
Jasper is a senior from Portland, Maine who is studying Mechanical Engineering Technology while pursuing a minor in Computer Science at the University of Maine. In his free time he enjoys playing cards, video games, and staying fit at the gym.
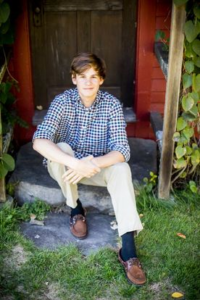
Kyle is a senior studying Mechanical Engineering Technology and pursuing a minor in Electrical Engineering Technology at the University of Maine. Kyle graduated from Nipmuc Regional High School in Upton, Massachusetts and enjoys playing hockey and guitar in his free time.
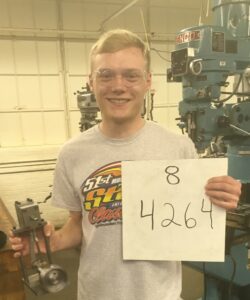
Xavier is a senior here at the University of Maine majoring in Mechanical Engineering Technology. He attended the university after graduating from Mt. Abram High School, a small school located in rural Western Maine. He grew up in an automotive racing family and enjoys his free time by spending it in the garage as well as his generational camp.
Project Overview
Our client has tasked us with retrofitting his son’s current helmet with a brake light and impact sensor in order to increase the safety of bicycle riding for his son. To start, the brake light must have different brightness levels that correspond to the rider’s braking force meaning that the harder the rider presses on the brakes, the brighter the light will become. Secondly, the impact sensor must be integrated into the helmet that is able to determine if the helmet is still safe for use after a crash. Our team will be using accelerometers, Arduinos, and 3D printing to achieve a product that is safe, weatherproof, and comfortable.
Weekly Updates
11/7/2020: Arduino code was reworked such that the sampling rate of the accelerometer was reduced and allowed for more steady light outputs. This also allowed for the Arduino to respond faster as there is now less data processing needed.
11/14/2020: Playdoh modeling was conducted on the helmet to give a basic shape of the vent we plan on placing the electronics in. This also gives us a way to dimension this void for the next steps in our project.
11/21/2020: Helmet was further disassembled and the use of other vents for hardware storage was considered. A second housing to be form fit within an upper vent was measured dimensionally for solid modeling. Further coding was also filtered and written for a better operating brake light. Lastly dimensioned drawings were created for the top and bottom vent solid model prototype.
11/28/2020: A low pass filter was added to the microcontroller program along with running median library to stabilize the input data received by the accelerometer and gyroscope. Top and bottom 3D printed housings which contain all the operating hardware were created this week as well.
1/29/2020: A prototype snap fit fastener used to attach the 3D printed housings to the helmet was designed and test printed. An updated top vent housing was also printed, being more ergonomic it reduces unusable space in the vent, while appearing aesthetically pleasing.
2/5/2021: A updated bottom vent housing was reprinted improving upon the previous prototype by lessening the wall thickness making it more spacious for electronics to be mounted internally, while also fitting tighter and appearing aesthetically pleasing.
2/12/2021: Both the arduino Nano and Uno are being programmed simultaneously to work out any bugs. Meanwhile the upper and lower vents are being prepped to receive heat-set inserts to secure them to the face plate. This will be accompanied by the adhesive neoprene gaskets which will waterproof the device.
2/19/2021: The cover plate was printed and assembled with the upper and lower housings. A test fit is shown below.
2/26/2021: Wiring cavities were added to the updated snap fit cover plate for easy assembly and wiring maintenance. These cavities will be used to pass wires from the top housing down to the bottom housing, as well as the exterior LED light. An updated version inclusive of these cavities has been printed and tested for fitment.
3/5/2021: All the 3D printed parts were assembled using heat-set inserts and adhesive neoprene gaskets. The accelerometer and arduino circuit was refined to operate on a battery, at the same time some major errors in the coding were re-written making the brake light function much better. This includes not turning on when turning the helmet left to right or due to minor bumps in the road.
3/12/2021: Technical drawings were created for all of the parts used in the assembly of the bicycle brake light, along with detailed wiring schematics for the arduino board, accelerometer, battery and lights. A design review was conducted on the current product.
3/19/2021: Standoffs were designed and printed as an addition to the bottom vent housing, these will be used to secure the arduino and accelerometer into place. The snap fit cap when attached will hold the arduino and accelerometer from sliding out once they are slid into the shelf style standoff.
3/26/2021: The top vent housing was redrawn and printed making use of heat set inserts located at the outside edges of the housing, rather than the original single insert located in the center. Effectively eliminating the flexure of the cap due to gasket compression forces.
4/2/2021: New fastener holes were relocated within the snap fit cap, along with some wire passageways to allow the battery cables and LED light wiring to pass through the cap. The snap fit portion of the cap was also extended, making it stand off from the helmet more to compensate for the needed depth in the top vent housing.
4/9/2021: The light was disassembled and reassembled with 3.7v LED light strips internally. This was done to compensate for the low voltage battery used in this application. De-soldering was performed on the arduino nano, along with some slight changes to shelving used in the bottom vent housing.
4/16/2021: A new snap fit cap was printed to accommodate gasket sealability for the LED brake light. On/Off switches were purchased and the installation process was started.
4/23/2021: The top vent housing was revised creating more internal room to accommodate two 3.7v batteries instead of just one. The snap fit cap was also adjusted for the simplicity of wiring. The assembly was then road tested to test overall functionality.
4/30/2021: The final assembly consisted of two, 3D printed housings attached to the helmet by a snap fit cap. Within the housings, an Elegoo Arduino Nano, MPU 6050 Accelerometer, and two 3.7V lithium ion batteries controlled and powered the brake light. A LED brake light was mounted upon the snap fit cap along with a on/off power switch.
Special Thanks
Alex Barrie – Client
Peter Howorth – Team advisor