Projects
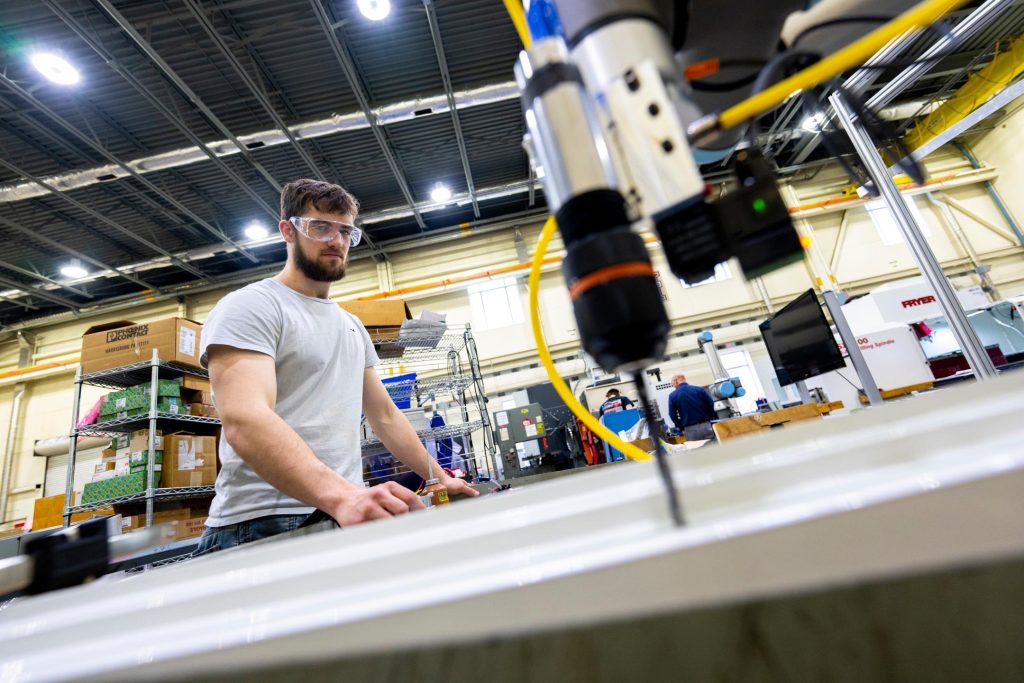
Partner With Our Students On Advanced Manufacturing Projects
A Few of Our Projects
LEARN MORE!
The Student Connection
Meet the next generation of innovators.
At the AMC, students work directly on client projects with hands-on support from expert staff. They deliver real results while gaining the skills needed to strengthen Maine’s workforce.
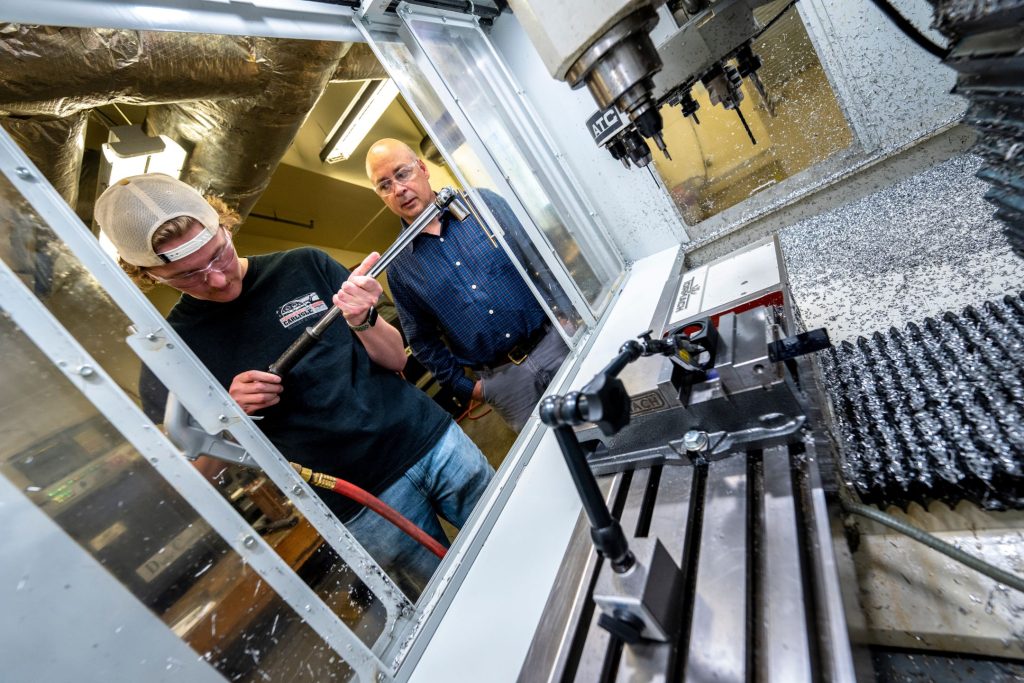
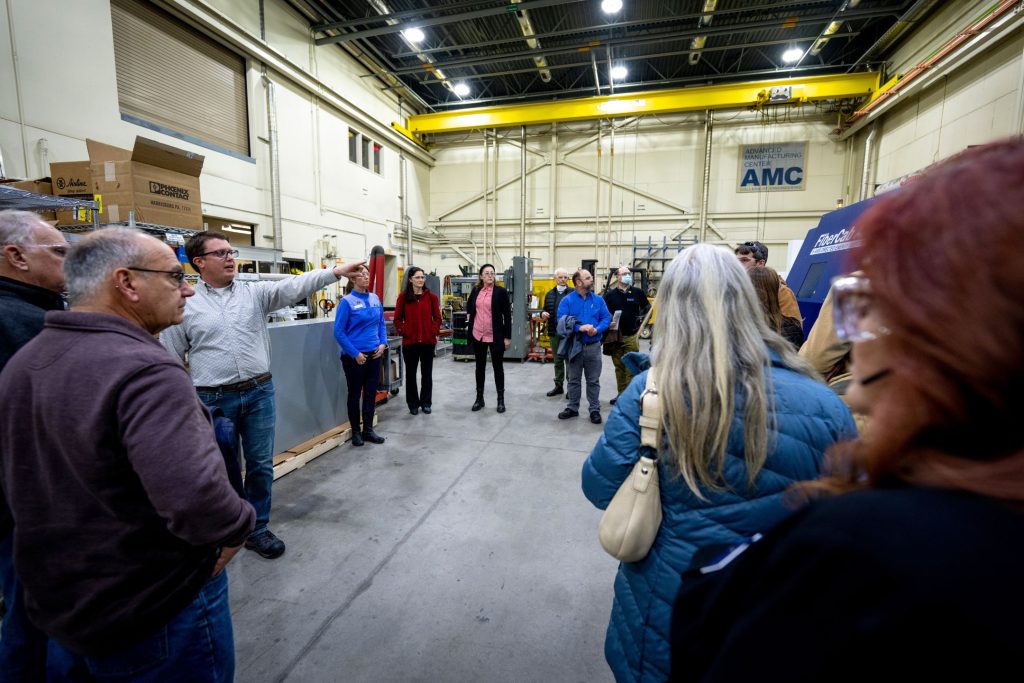
Facilities
Advanced tools for advanced solutions.
Our center includes collaborative robots, precision CNC machines, composite fabrication labs, and full prototyping capabilities. Clients access the same technology used by top manufacturers.
Partnerships
Collaboration that delivers results.
We work with startups, small businesses, and established manufacturers to solve real-world challenges. By combining university expertise with industry needs, we deliver practical, scalable solutions.
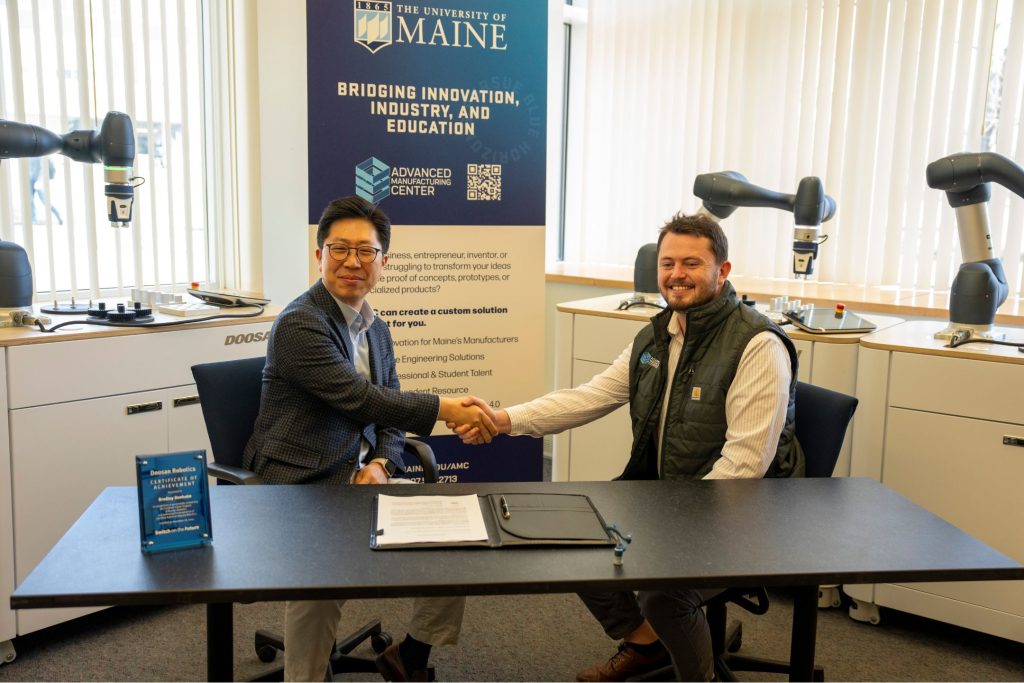
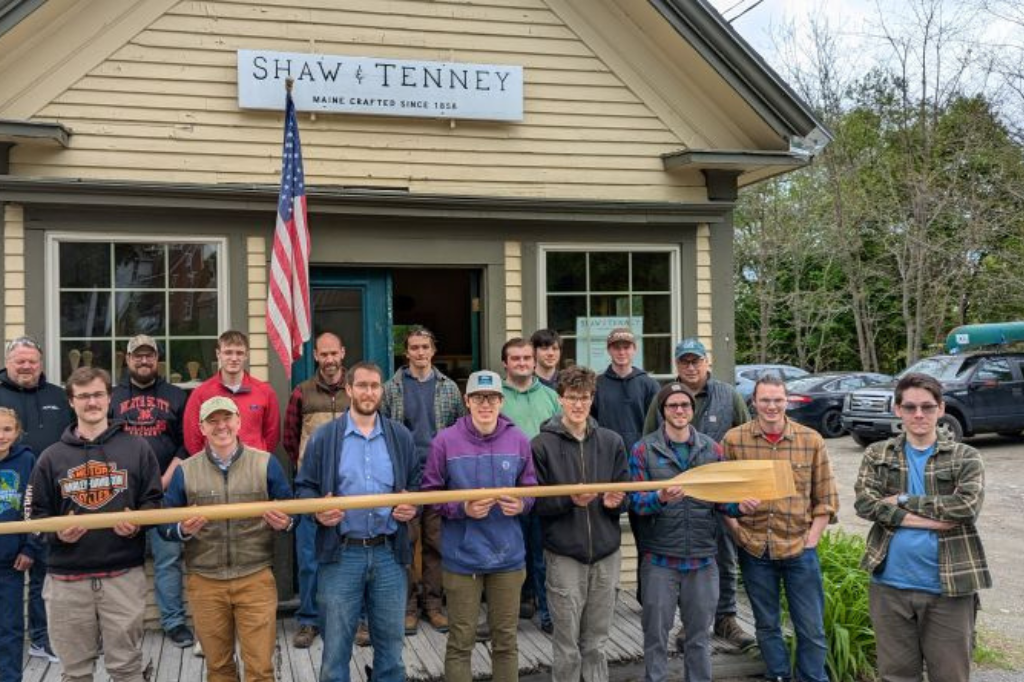
Staff
Experienced. Dedicated. Results focused.
Our team brings decades of experience in engineering, design, and manufacturing. Every project is guided by professionals committed to quality and impact from start to finish.