About the Class
The Six Sigma program at the University of Maine consists of Six Sigma and Lean Manufacturing training within MET 320 “Six Sigma,” which is taught once per year. Students may earn a University of Maine
College of Engineering Six Sigma Green Belt (SSGB) Certificate by successfully completing an industry-sponsored project, passing a cumulative exam, and completing MET 320.
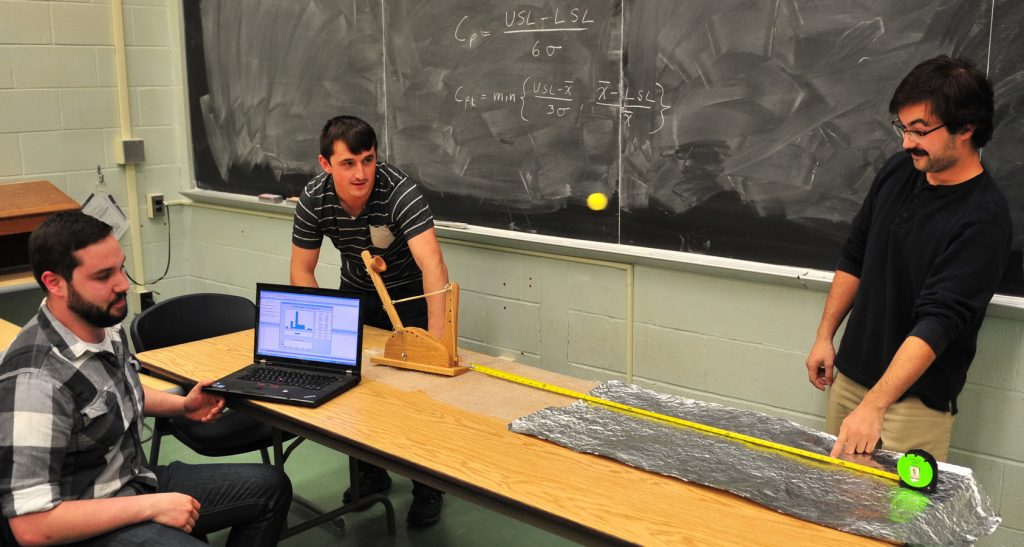
Six Sigma
Six Sigma is a continuous improvement methodology intending to increase profitability by driving defects to extremely low levels. The name Six Sigma is derived from the desire for the process mean to be 6 standard deviations, or 6 sigmas, from the nearest specification limit. Six Sigma projects are couched upon the Define-Measure-Analyze-Improve-Control (DMAIC) model and have resulted in billions of dollars of savings per year1.
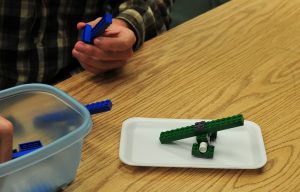
Lean Manufacturing
Lean Manufacturing is a continuous improvement methodology intending to increase the rate at which value is added to a product or service. To increase profitability, Lean Manufacturing seeks to reduce the 7 forms of waste, or muda (i.e., defects, overproduction, transportation, waiting, inventory, motion, and (over)processing).
MET 330 “Six Sigma”
MET 330 “Six Sigma” is a technical elective within University of Maine’s Mechanical Engineering Technology and has been recognized as a technical elective within other University of Maine College of Engineering programs. The class consists of independent assignments, in-class lectures, and in-class hands-on learning activities, such as lean factory simulations, Gage Repeatability & Reproducibility (Gage R&R), process capability, and design of experiments. The Six Sigma Green Belt program is accredited The Council for Six Sigma Certification (CSSC).
Selected MET 330 Course Topics
- Lean Manufacturing — 7 forms of muda, continuous flow manufacturing, value stream mapping, 5S, value added and non-value added activities
- Define — Project selection, Voice of Customer (VOC), project charter, Kano analysis, Supplier Input Process Output Customer (SIPOC) analysis
- Measure — Data types, defects per million opportunities (DPMO), Gage R&R, Measurement Systems Analysis (MSA), accuracy/precision, confidence intervals, Z-distributions, t-distributions, capability analysis
- Analyze — Pareto analysis, correlation, linear and non-linear regression, hypothesis testing, ANalysis Of VAriance (ANOVA), Ishikawa diagrams
- Improve —Full and fractional factorial Design Of Experiments (DOE)
- Control — Statistical Process Control (SPC)