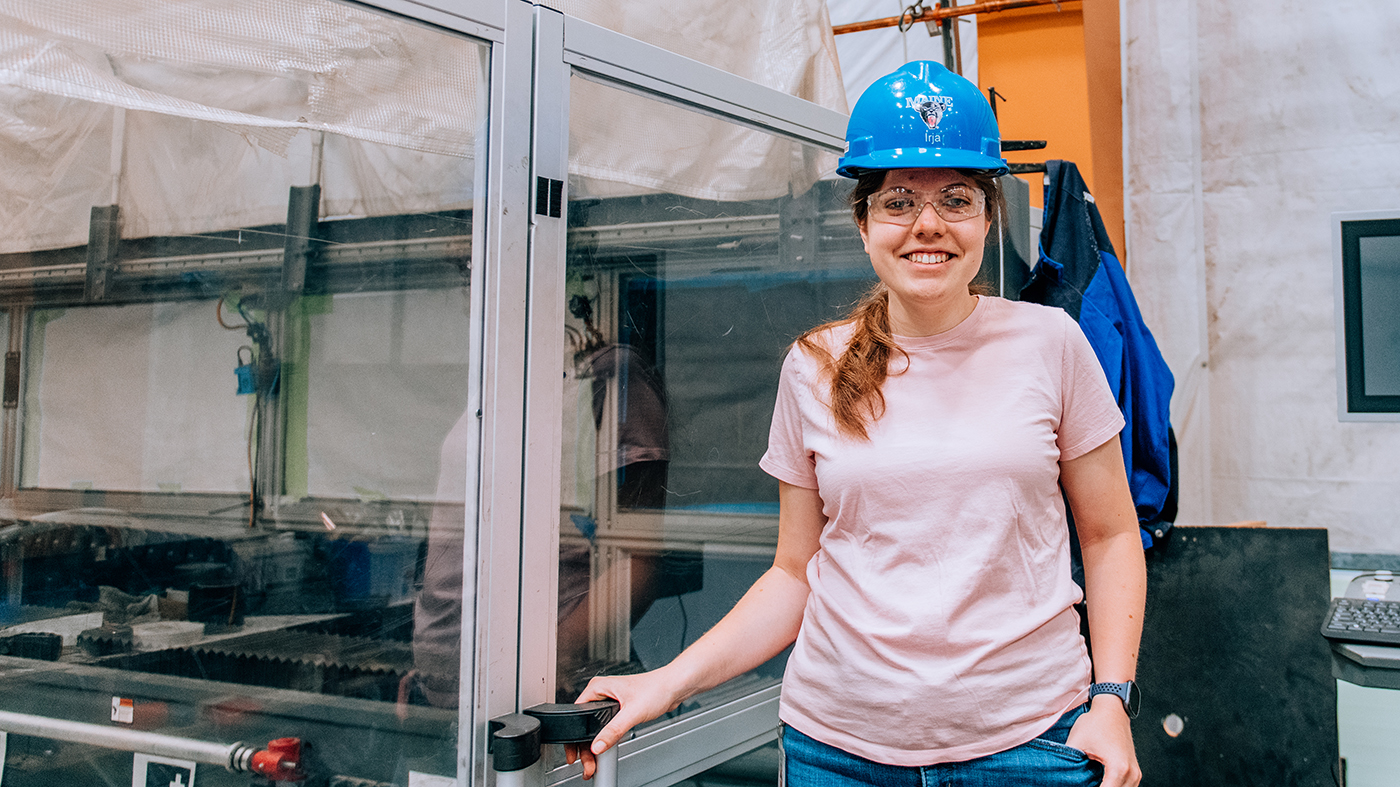
Irja Hepler: Tackling thermal stress in 3D printing
Irja Hepler wants to crack the code on the additive manufacturing cooling process to make 3D printing faster, stronger and more precise.
The University of Maine Ph.D. student in structural engineering is developing code to improve her model that predicts how thermal stress created during 3D printing could change what is being printed. Once developed, this model has the potential to allow those using 3D printers to change how they print their projects to prevent thermal stresses and create more structurally sound objects, whether it be a violin or a house.
UMaine, which currently houses the world’s largest 3D printer and is working to expand these capabilities, is at the forefront of research and innovation in additive manufacturing at an unprecedented scale.
In 2014, while attending the Maine School of Science and Mathematics (MSSM), Hepler secured an internship in Russell S. Bodwell Distinguished Professor Bill Davids’ aerospace transportation innovation project at UMaine’s Advanced Structures and Composite Center. Davids also chairs UMaine’s Department of Civil and Environmental Engineering and was a Distinguished Maine Professor in 2015.
The internship set Hepler down a path that introduced her to MatLab, a coding system used by engineers, and 3D printing, as well as encouraged her to complete her undergraduate, graduate and current Ph.D. at UMaine.
As part of Hepler’s Ph.D. work in Davids’ lab, she aims to create a model that would allow engineers to predict how thermal stresses may change the shape of a printed part. 3D-printing technology has introduced a wide range of new possibilities, from hobby projects to precision engineering, but it can become expensive and finicky, with materials easily wasted if printer settings are not correct. This has a lot to do with how printed projects cool while being made.
“Because of differential cooling, you get thermal stresses,” explained Hepler. “These stresses get locked in. When you finish the part and take it off the bed, it has these stresses in it, and these initial stresses cause the part not to behave normally.”
Stresses can cause the printed object to be structurally weaker or even warped. Through a model like hers, Hepler hopes engineers can one day abandon the trial-and-error method of printing and reprinting by predicting what stresses could be caused by certain printer settings, and then changing those settings before attempting to print, saving time, money and resources.
A model similar to what Hepler wanted existed when she began her project, but it predicted outcomes based on 3D solid elements and could take three hours to run one scenario. In Hepler’s initial model, rather than cubes, there were beams, or lines, of material laid on top of each other in a 2D square. Hepler’s model runs one scenario in 15 minutes, significantly faster than the previous solid model, meaning engineers can analyze printer settings in a couple of days, rather than weeks, and then print a structurally sound object.
Hepler’s current project is a continuation of her beam model, which works only in 2D. She is now coding the model so it works in 3D to reflect the endless possibilities of 3D printing. While she has never written code for a 3D model before, Hepler is confident she will succeed. “I mean, 3D’s difficult, it’s very hard, but it’s just an extension of what the first model was,” she said.
Once Hepler completes her model in MatLab, she hopes that the code can be further improved by someone with a background in coding to make the model even faster and, eventually, give it a user interface so it is easily accessible for anyone attempting to 3D print.
Hepler plans to finish her Ph.D. in the spring of 2026, but she hopes her model will be used for a long time after. Hepler envisions UMaine using her model to help print structurally sound houses without thermal stresses at a quicker and more efficient rate to combat the housing crisis impacting Maine.
“Research is just really important. It could help lots of people,” Hepler said. “Even if it’s slow and sort of unsteady and goes in fits.”
Written by Emma Beauregard, Research Communications Intern
Contact: Erin Miller, erin.miller@maine.edu